Sustainable solutions for everyday use
Starting in their 2nd year, a number of engineering and automotive students spend a lot of time at Industry Park Kleefse Waard (IPKW) in Arnhem. They work there on projects to find sustainable solutions for everyday use. They also collaborate with students from other disciplines.
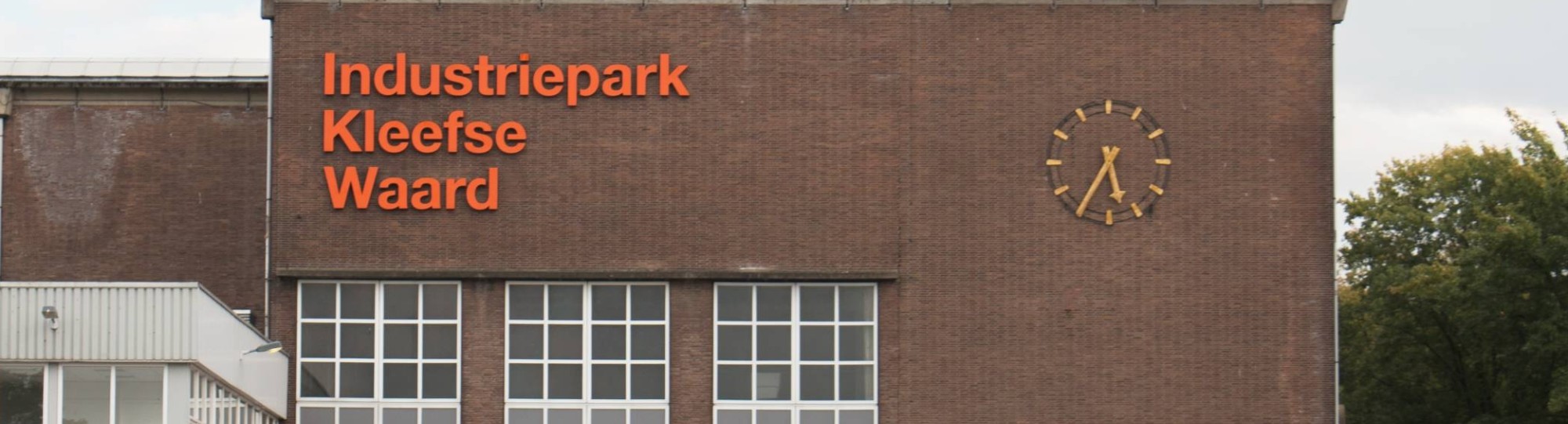
Collaborative projects
A project group can be large, consisting of 15-20 students. But there are also assignments that can be carried out by just 2 to 4 people. Some assignments are new. But a project group often builds on the work of an earlier student group.
The students are studying Electrical and Electronic Engineering, Mechanical Engineering, Industrial Design Engineering and sometimes Automotive Engineering or Industrial Engineering & Management. Because Electrical and Electronic Engineering, Mechanical Engineering and Automotive Engineering are also taught in English at HAN, some project groups communicate in English.
Curious about the projects? We’ve chosen 3 of them to put in the spotlight. These are just 3 of the many projects running from September 2019 to February 2020.
HPV project: transport without fuel or batteries
HPV stands for Human Powered Vehicle: a vehicle powered by human muscle power. The main drive of an HPV can be electric, but all the energy needed for this has to be generated by the user. So no batteries, no fuel, but pure nature.
Developing an HPV is quite a task. That’s why no less than 16 students are working on it. Four students from Industrial Design Engineering made the design for the HPV. Six Mechanical Engineering students are responsible for the construction. That’s a self-supporting bodywork built up from 3D printed elements. Six Electrical and Electronic Engineering students have divided their tasks according to specialisation. Industrial and Power Systems students are developing the main drive. And Embedded Systems students are making the smart user interface and the dashboard.
The client is designer Michiel van der Kley, a well known furniture designer and designer of the largest 3D printed concrete bicycle bridge in the world.
With 8 weeks down and just 16 to go, the students show the HPV in its current stage of development.
Skid: improving the work of an earlier student group
Because the Netherlands is moving away from natural gas, the heating installations in many houses will have to be adjusted in the near future. A heat pump is a logical alternative. Client Ordelman & Dijkman wants to develop a unit that can be assembled in the workshop. A unit with heat pump, heat exchanger, pipes, control systems and everything else that goes with it. The complete installation will then be brought to the construction site. In 1 go it will be placed under the roof of a newly built or newly renovated house. A ready-made unit like this is called a skid. Once in place, the pipes of the installation are connected to the pipes in the house.
Ordelman & Dijkman is getting students to develop the skid. At the moment 2 groups are working on the best method for placing the heat pump in the skid. A number of students are investigating whether and how the current heat pump can be built using the same main components. But then with an adapted design. Another group is looking into the communication between the heat pump and the other installation components. The students are building on the work of last year’s students, who were involved in the initial development.
Wattsun: the next step
During his degree in Industrial Design Engineering, Koen Olieslagers developed the Wattsun pop-up power. He also set up his company Wattsun. The Wattsun pop-up power is a stackable (modular) battery system. It can be used to temporarily provide energy to a certain location. Think of festival locations or construction sites. No noise, smell or CO2 emissions from diesel generators and no long cables. The advantages are clear.
That was in 2015. Koen is back at HAN, but now as an independent entrepreneur with a few interesting research assignments. He wants to further develop his battery systems.
The Control Systems Engineering research group has taken on the assignment and entrusted it to students Ivo Bosman and Noura Alboushi Aldabbagh. Both are studying Electrical and Electronic Engineering and are working in the Powerlab at IPKW on the following tasks:
- Researching the optimal charging and discharging system for the existing Wattsun battery system;
- Working out how you can connect multiple modular battery systems to the power grid and how they can best be controlled;
- Determining which type of PV panel (=solar panel) and charging system is the most suitable for off-grid application (so separate from the mains) and that best suits the existing Wattsun concept (modular, portable and plug & play).